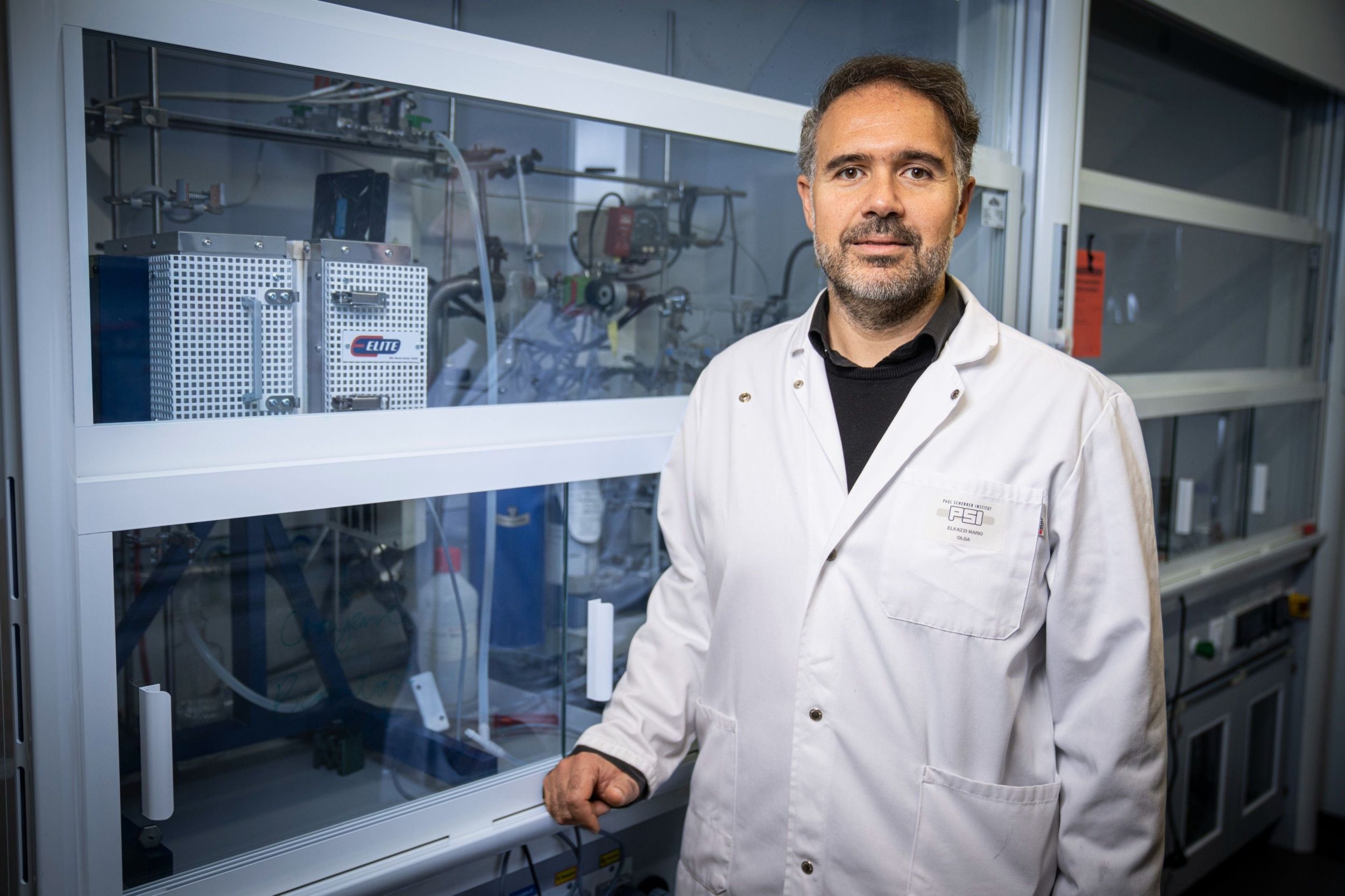
Neue Schutzschicht macht Akkus von Elektrofahrzeuge leistungsfähiger – und trägt indirekt zum Klimaschutz bei
Sie stecken in Mobiltelefonen, Laptops, Elektrowerkzeugen, Elektroautos und stationären Energiespeichern: Lithium-Ionen-Akkus, die als Schlüsseltechnologie für die Dekarbonisierung gelten. Deswegen arbeiten Forschende weltweit daran, deren Leistungsfähigkeit fortlaufend zu verbessern; unter anderem durch eine Steigerung der Energiedichte.
«Eine Möglichkeit, dies zu erreichen, liegt darin, die Betriebsspannung zu erhöhen», sagt Mario El Kazzi vom Zentrum für Energie- und Umweltwissenschaften am Paul Scherrer Institut PSI. «Steigt die Spannung, so steigt auch die Energiedichte.»
Jedoch gibt es da ein Problem: Bei Betriebsspannungen von über 4,3 Volt finden am Übergang von Kathode, dem Pluspol und dem Elektrolyten, dem Leitmedium, starke chemische und elektrochemische Abbauprozesse statt. Deswegen laufen kommerzielle Batteriezellen, zum Beispiel die von Elektroautos, bisher auch nur mit maximal 4,3 Volt.
Um dieses Problem zu lösen, haben El Kazzi und sein Team eine neue Methode entwickelt, mit der sich die Oberfläche der Kathode stabilisieren lässt, indem diese mit einer dünnen gleichmässigen Schutzschicht überzogen wird.
Betriebsspannungen von bis zu 4,8 Volt
Im Mittelpunkt des Verfahrens steht ein Gas, das bei der Herstellung von Kunststoffen wie PTFE, PVDF und Schaumstoff als Nebenprodukt entsteht: Trifluormethan. Im Labor leiteten El Kazzi und sein Team bei 300 Grad Celsius eine Reaktion zwischen diesem Gas und der dünnen Schicht aus Lithiumkarbonat ein, welche die Oberfläche der Kathoden bedeckt. Dabei wandelt sich das Lithium an der Grenzschicht in Lithiumfluorid (LiF) um.
Wichtig dabei: Die Lithium-Atome des Kathodenmaterials bleiben dabei als Ionen erhalten, also als positiv geladene Teilchen. Diese Lithium-Ionen müssen nämlich beim Laden und Entladen zwischen der Kathode und der Anode, dem Minuspol, weiter hin- und herwandern können, damit die Akkukapazität im späteren Betrieb nicht beeinträchtigt ist.
In einem weiteren Schritt prüften die Forschenden die Wirksamkeit der Schutzschicht: Die Schutzschicht blieb auch bei hohen Spannungen stabil. Sie schützt das Kathodenmaterial so gut, dass Betriebsspannungen von 4,5 und sogar 4,8 Volt möglich sind.
Im Vergleich zu Batterien mit ungeschützten Kathoden schnitten die beschichteten bei allen wichtigen Parametern deutlich besser ab. «Ein eindeutiges Zeichen dafür, dass unsere Schutzschicht den Anstieg des Widerstandes abschwächt, der durch die sonst stattfindenden Grenzflächenreaktionen auftritt», erklärt El Kazzi.
Verglichen wurde auch der Kapazitätserhalt. Auch hier erwies sich der Akku mit beschichteter Kathode in den Tests als überlegen: Der Kapazitätserhalt lag bei über 94 Prozent nach 100 Lade- und Entladedurchgängen ohne Abnahme der Ladegeschwindigkeit, während der unbehandelte Akku auf nur 80 Prozent kam.
Universelle Lösung mit indirektem Klimaschutz
Das am PSI entwickelte Beschichtungsverfahren öffnet neue Wege, die Energiedichte von verschiedenen Batterietypen zu steigern: «Wir können davon ausgehen, dass unsere Lithiumflorid-Schutzschicht universell und bei den meisten Kathodenmaterialien anwendbar ist», betont El Kazzi.
Ein weiterer wichtiger Aspekt des neuen Verfahrens: Trifluormethan ist ein hochwirksames Treibhausgas und mehr als 10’000-mal klimaschädlicher als Kohlendioxid, weswegen es keinesfalls in die Atmosphäre gelangen sollte. Für El Kazzi stellt die Umwandlung in eine einheitliche dünne LiF-Schutzschicht auf der Oberfläche von Kathodenmaterialien eine effiziente Lösung dar, das Gas zu monetarisieren, indem es Teil einer Kreislaufwirtschaft wird. Mit dem neuen Beschichtungsverfahren lässt sich das Gas recyceln und als Schutzschicht in Hochspannungskathoden langfristig binden.